Optimizing Filter Houses in Gas Turbines
How to recover performance for Gas Turbine generators
Background
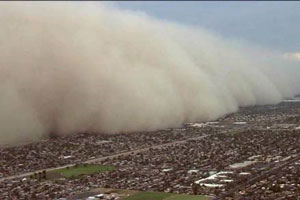
The challenge for the powerplant OEM when offering a new gas turbine system is to be cost competitive in the context of a large capital investment for the user. There are several standardization decisions made that deliver a somewhat generic design and implementation. In this process, some of the technical features affecting performance of the filters can be missed.
The analogy to automobile production is quite relevant. Business users of pickup trucks may wish for improvements in torque or gearing to handle local conditions but are unwilling to pay the premium for a custom design. Continuing the analogy, the auto aftermarket exists to supply special or niche improvements to standard equipment to meet the customer need, once they have identified the actual conditions needed and calculated the ROI.
Owners of power generation plants have an opportunity, often in the light of operating experience over time, to react to changing needs or to remedy performance deficiencies by upgrading and retrofitting the filter house.
Needs
Pressure drop across the filter bank remains the core measurement of performance. In the original filter house design, pressure drop was probably allowed to be as high as possible while still meeting the rated output and efficiency. There may have been minimal attention paid to expected life-cycle costs such as filter change frequency or filter media selection to address harsh dust loads or other environmental parameters.
It is possible that filter cleaning methodologies were overlooked. Pulse-cleaning systems have become ubiquitous across the industry yet there are other options to consider once a thorough analysis of the environmental conditions is completed.
Generally, the power plant operator wants to maximize filter life, reduce compressed air costs and minimize damage to the turbine. In addition, he may want to maximize uptime in extreme weather scenarios such as snow and ice.
Maximizing filter life is driven by the cleaning pulse control strategy and the total air volume of the filter house. In the case of a “static” filter house, the presence of abrasive dust, ambient chemical contaminants and irregular maintenance might suggest that using a pulsing system would be more effective.
Compressed air costs do not consist only of generation of the pulsed air, they include replacement and service of valves and maintenance of the compressors. There is rarely any attention paid to pulsing control; rather, the user is conditioned to think that bag changes are inevitable.
Striking a balance of filter media choice, cleaning system and control and filter house design will lead to reduced particle damage to the turbine and improved efficiency.
Options
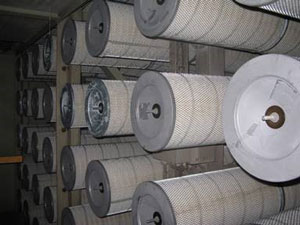
As a user develops experience of filter house operation, he will gain a stronger understanding of the potential savings and efficiency improvements needed. Replacing the filter house is of course a costly capital project but, if there is structural wear and other issues, the cost of filter replacement alone might justify it.
This is because a skilled filter house design team can unearth output, efficiency and filter life gains. Typically, a larger filter house reduces pressure drop and the gains are considerable because they are non-linear. For example, a 20% increase in flow can produce a 40% increase in filter life.
Next, the operator should consider the conversion of a static filter to pulse cleaning. If the dust environment or the ambient pollution is casing degradation of the turbine, the conversion cost can far outweigh the repair, re-build or replacement cost of the turbine.
While considering upsizing or conversion of the filter house by a filtration expert, there are other topics to discuss that might enhance the plant ROI. These are; Introducing evaporative cooling to the inlet filter system or changing to an inlet chilling strategy. Both can provide rapid ROI by significantly increasing the generated electrical output and thus the revenue for the plant.
Cooled or chilled air is denser; therefore the higher mass flow is combined with more fuel for higher turbine output. Of the two options, chilling allows for greater temperature drop and therefore higher output than evaporative cooling but at a much higher investment level.
Chilling has the added advantage of providing the higher output independent of weather, so the greater energy output is available for more operating hours per year than evaporative cooling.
Example
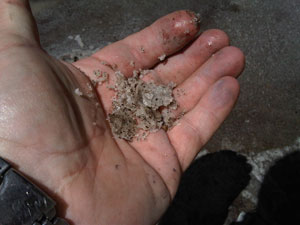
An owner-operator constructed a power plant with a single Siemens 501FD3 turbine, entering operation in 2009. The plant was located immediately adjacent to the Pacific Ocean. The site experienced daily salt-laden fog from the sea during at least 6 months of the year. For the other 6 months it was common to have “Santa Ana” winds with heavy dust loads blowing from the inland direction.
Humidity was always high with condensing conditions almost daily. Shortly after commissioning, the turbine crashed in a catastrophic failure. Investigation found large amounts of salt collecting in the clean air plenum downstream of the filters as well as into the turbine compressor.
The initial plant design had only included the most basic static filter system with a typical two stage static filter. The inlet filter was sized at the minimum allowable by the OEM specifications for the defined inlet flow rate of 890,000 acfm. Filter elements were specified by the OEM at standard construction and performance levels for that turbine model.
The initially installed pre-filter was a 24 x 24 x 4” deep pleated element in a “beverage board” frame. However, the media had no water repellant properties and the efficiency level was only G3. The final filter initially supplied was a V-cell type using plastic frame components and glass microfiber media.
As permitted by the OEM specification, the filter efficiency was only MERV 11 with no specific water repellant properties. Filters had to be changed every month during the Santa Ana winds season due to high pressure drops which resulted from condensed moisture and high dust loads on the filters. Filter changes often required outages and lost revenue for the plant.
A solution was developed to replace the existing filter inlet system with a multi-stage self-cleaning pulse type filter system. The filter house size was significantly increased to allow for improved pulse cleaning ability and to increase the life of the filters.
The new first stage filter elements incorporated a 100% synthetic media and included a highly water repellent layer on the air entering side. Filter efficiency was increased from MERV 11 to MERV 15. All metal components (end caps and screens) were stainless steel. Downstream of the pulsed filters, additional safety filters for potential coalescence of large droplets were installed.
As a result, the system has eliminated the migration of salt into the turbine, totally protecting it. There have been no further outages for compressor, internal turbine maintenance or washes. Additionally, the pulse filters have lasted more than 4 years in service and without a scheduled change in sight.
Conclusion
Operators of existing power plants can take advantage of solutions available from expert providers of filter houses to gain a rapid ROI and an improvement in operating output. They can realize increased filter life and reduced operating costs by focusing on filter house designs that are customized to the actual operating conditions and sized accordingly.
ROI is more attractive than often thought. An in-depth review and proposal can be sought from a filtration expert in order to rejuvenate older units or those with challenging environmental conditions.
Contact us to create your custom solution
Call us at: 704-859-2723 or fill out the form below.